Heat Exchangers
Do you like free heat? We do. The recuperator recovers heat from the hot gases of a turbine cycle to heat the air before entering the combustor. This reduces the amount of new fuel consumed increasing the thermal efficiency of the turbine system.
Brayton has 30 years of experience in the most challenging heat exchanger applications using patented recuperator technologies. Brayton has designed and developed a variety of recuperator architectures in diverse shapes, sizes and materials.
Technical Expertise
- High temperatures (600 to 1100°C) operating conditions.
- Pressures from 3 to 300 bar, and environments involving high thermal gradients and transients.
- Supercritical CO2 cycles
- Advanced micro-channel and micro-pore surfaces.
- Advanced manufacturing methods
- Metallurgical analysis of metal bonding and welding methods
- Surface characterization
- Component level in-house qualification testing; hydrostatic, creep, friction and joules (F&J) characterization.
Approach
Heat Exchanger Technology


Heat Exchanger Design and Test Facilities
Heat Transfer Test Rig
Brayton’s F&J (friction and joules) test rig provides thermal characterization for heat exchanger sub components including pressure drop and heat transfer characterization. Engineering can determine critical fin metrics such as density (number of folds per in), foil thickness, flow length and the performance of different fin configurations.
Thermal Fatigue & Creep Test Rig
- Pressure up to 103 MPa (15,000 psig)
- Temperature up to 850°C (1562°F)
- Samples measured within tight process control, with the following tolerances:
- Temperature: ± 12.7 °C
- Fin and plate Thickness ±0.0002”
- Pressure: (gage) ± 1 psi (6.9 kPa)
- Fin density ± 0.5 fpi
- Time: ± 0.5 min
High-flux thermal & Aerodynamic Test Rig
High-flux thermal and aerodynamic test rig.
- Measuring friction factor and heat transfer coefficient
- Measure pressure losses
Prototype assembly and Pilot Manufacturing Facility
$1M Capital & Tooling Investment
Complete recup fabrication
- Stamped plate assembly
- Braze prep
- Auto core welding
- Vacuum brazing and diffusion bonding
- High-density fin tooling and wire matrix weaving
- Quality testing
- 28,000 SF facility
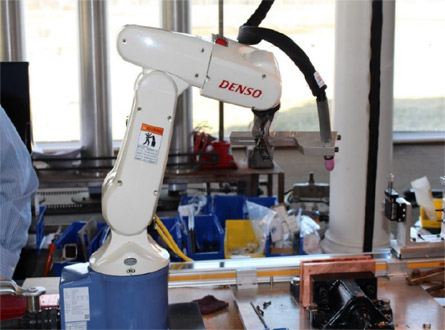
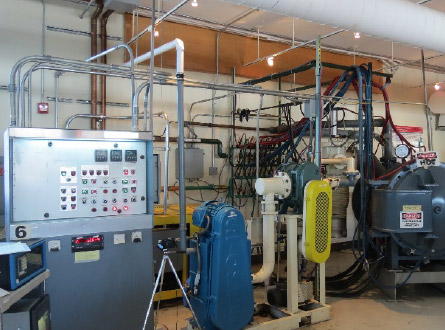
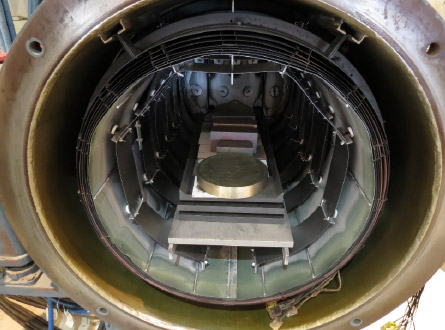

Custom HX Manufacturing:
